Hot-dip galvanizing:
Hot-dip galvanizing process line equipped with tubs with dimensions:
13000 x 1600 x 3300 mm.
Maximum dimensions of galvanized components:
12500 x 1500 x 2800 mm, unit weight up to 9 tons.
The galvanizing offered is hygienically certified.
Galvanizing:
Gloss and matte coating, colorless or colored passivation.
Zinc is the thirtieth element in Mendeleev’s periodic table (atomic number Z=30), but number 1 on the list of most durable corrosion protection. It is a silvery metal with a melting point of 419°C. As a micronutrient, it is essential for living organisms, plays an important role in the metabolism of humans and animals, and is responsible for the good functioning of the sense of sight and the immune system, among other things. Zinc can be found in medicines, car tires and plastics, and as a pigment in paint products. Galvanized sheet metal covers roofs, and gutters and facade covers are made of it. Among the numerous uses of zinc, the protection of steel against corrosion by hot-dip galvanizing comes to the fore.
Hot-dip galvanizing Poznan
Hot-dip galvanizing is an immersion method. This means that both surface preparation and zinc coating are carried out by immersing structural elements in baths that contain baths of the appropriate chemical composition. Such technology ensures that every crevice can be reached, cleaned and protected against corrosion. The final stage of the galvanizing process is the application of zinc coating to clean steel components, which are immersed in molten zinc. The working temperature of the zinc bath is about 450°C. A rapid reaction between iron and zinc then takes place, which leads to the formation of a zinc coating on the steel surface. Its structure and properties depend on the chemical composition of the steel substrate, as well as its thickness and design. With the fulfillment of certain conditions for the grade of steel, especially it is about the content of silicon and phosphorus, as well as with the appropriate construction of the elements to be galvanized, anti-corrosion coatings resistant to mechanical damage, abrasion, erosion, impact, free of porosity, showing excellent adhesion to the substrate are obtained.
Hot-dip galvanizing technology uses the phenomenon of diffusion, which involves the “penetration” of zinc atoms into the outer layer of steel during a “bath” in molten zinc. In this way, an iron-zinc alloy is formed on the surface of the steel component. When the galvanized workpiece is removed from the zinc bath, a layer of pure zinc remains on the outer surface of the alloy. The zinc coating obtained in the hot-dip galvanizing process has a layered structure. It consists of alloyed, iron-zinc phases and a layer of pure zinc. The presence of alloy layers makes the zinc coating inseparable from the steel substrate. This is a very important feature if one takes into account the fact that steel components are exposed to significant surface loads during transportation, assembly and further use, which coatings bound to the substrate by physical adhesion effect alone cannot withstand.
The anti-corrosive properties of zinc coatings lie in the fact that zinc can form extremely resistant and hardly soluble opaque coatings. They form when they come into contact with air and water. They consist mainly of basic zinc carbonate and are responsible for proper corrosion protection. Although they are worn away in small amounts over the years by wind and atmospheric influences, they are formed anew due to the zinc beneath them.
Fire zinc coating provides not only passive protection as a physical barrier shielding the steel, but also electrochemical protection because zinc, as a more active metal, oxidizes itself, protecting the steel from this.
The zinc coating protects the steel for many years and does not require maintenance. In addition, it is possible to extend its life and give the products the desired aesthetic qualities by covering the galvanized surface with an additional varnish or paint coating (the so-called duplex system).
Coating thickness
The hot-dip galvanizing process produces coatings with an average thickness of 70 to 150 micrometers. This thickness is sufficient to protect the steel from corrosion for decades. The average life of a zinc coating is 30-50 years.
The thickness of the zinc coating is measured in micrometers or the weight of the coating is given in g/m2.
The minimum coating thicknesses recommended depending on the thickness of the material from which the galvanized parts are made are specified in EN ISO 1461:
Thickness of steel (t) in mm | Minimum average coating thickness in ľm | Mass related to the surface in g/m2 |
---|---|---|
t ≥ 6 mm | 85 | 610 |
3 mm ≤ t < 6 mm | 70 | 505 |
1.5 mm ≤ t < 3 mm | 55 | 395 |
t < 1.5 mm | 45 | 325 |
The thickness of the coating depends on the following factors:
- thickness of the steel,
- the chemical composition of the steel; in particular, the content of the elements silicon and phosphorus; the content of silicon in the steel to be galvanized should be less than 0.03% (with a total content of silicon and phosphorus not exceeding 0.045%) or from 0.15% to 0.24% silicon (with a total content of silicon and carbon less than 0.5%),
- the temperature of the zinc bath and the length of time the component is held in the zinc bath,
- the surface roughness of the component.
Durability
Durability refers to the length of time the zinc coating exists in sufficient quantity to protect the steel from corrosion. As time passes, oxidation of the coating occurs, causing the upper zinc layers to disappear and the iron-zinc alloy layers to be exposed. As long as there is zinc in these layers, it provides protection against corrosion.
The life of a zinc coating depends on the corrosive load of the environment in which the structure is operated, as well as the thickness of the coating.
The durability of coatings can be calculated by a simple mathematical operation (EN ISO 14713):
(Thickness of zinc coating in ľm / Consumption of zinc coating in ľm per year) = Protection in years.
According to this calculation, for a coating thickness of 70 ľm, the following durability periods can be determined depending on the corrosivity category of the atmosphere:
Corrosivity category PN-EN ISO 12944-2 | Corrosion load atmosphere corrosivity | Annual thickness loss of zinc coating in ľm | Protection in years |
---|---|---|---|
C1 (very low) | Negligible – interiors of air-conditioned buildings | ≤0,1 | >100 |
C2 (small) | Low – atmosphere with low pollutant content and dry climate; mainly rural areas | > 0.1 to 0.7 | 100 |
C3 (medium) | Moderate (moderate coastal climate, urban atmosphere with medium SO2 pollution) | > 0.7 to 2.1 | 30÷100 |
C4 (high) | High (industrial and coastal areas with medium salinity) | > 2.1 to 4.2 | 17÷30 |
C5 (very high) (C5-I, C5-M) | Very high (industrial areas with high humidity and aggressive atmosphere and coastal areas with high salinity) | > 4.2 to 8.4 | 8÷17 |
Mechanical strength
The protective coating produced by the hot-dip galvanizing process is built up in layers. Very hard zinc-iron alloy layers, harder than steel, are formed at the surface of the component. The outer layer of the coating has a chemical composition similar to that of the zinc bath, its hardness corresponds to that of zinc. This structure of the zinc coating makes it resistant to mechanical damage, as the outer soft layer absorbs pressure and impact, and the inner hard layer protects the substrate from damage.
Aesthetics
The appearance of the zinc coating is influenced by:
- the chemical composition of the substrate material,
- Technologicality of the structure,
- geometric shapes and the weight of the component,
- the parameters of the galvanizing process.
The quality and appearance of the coatings obtained depend on the chemical composition of the steel, and in particular on the content of carbon, phosphorus and silicon.
Steel with a silicon content in the critical range from 0.03 to 0.15% and above 0.3%, after galvanizing has a gray-colored, rough, uneven and brittle surface (in principle, it should not be galvanized).
When joining parts that differ in heat capacity, parts with higher heat capacity may have a gray surface, and parts with lower heat capacity, a metallic glossy surface.
Cost
Due to the many years of corrosion protection provided by hot-dip zinc coating, it is a very economical protection. The costs incurred at the time of coating in relation to the life of the coating turn out to be negligible.
The total costs of the corrosion protection system include: execution costs and repair costs. The authoritative factor in calculating costs is the durability of the corrosion protection. The following table shows a comparison of hot-dip galvanizing with two paint systems, a more expensive and a cheaper one.
Table: Comparison of cost components of hot-dip galvanizing with painting
Operation | Painting system 1 | Painting system 2 | Hot-dip galvanizing |
---|---|---|---|
surface preparation | manual | mechanical abrasive blasting | included in the price |
primer coat | 1 | 1 | – |
topcoat | 2 | 2 | zinc, 85 µm |
durability | 8 years | 11 years | 50 years |
repair | every 8 years | every 11 years | – |
performance and repair costs in % | 198 | 169 | 100 |
Hot-dip galvanizing turns out to be a more economical solution. The proof is simple: the application of paint coatings is a very labor-intensive, and therefore also expensive in terms of execution costs, operation that must be repeated every few years. Future costs arise mainly due to the short life of the paint coating compared to the zinc coating, which involves maintenance painting. Hot-dip zinc coating does not require this. Therefore, the cost of hot-dip galvanizing remains the same, while the cost of protecting with a paint coating increases staggeredly over time due to repairs performed every few years, as shown in the graph:
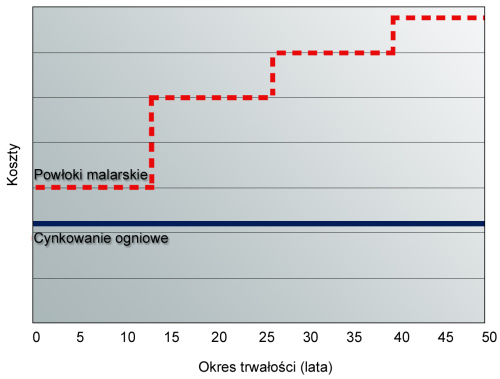
The paint coating ages relatively quickly. It becomes less and less flexible, cracks, scratches and peels. On average, it requires maintenance every 6 to 7 years, so the cost of such protection increases over time.
Zinc coating provides many years of protection of steel against corrosion without the need for renovation, which is an essential factor in determining its cost-effectiveness. The cost of hot-dip galvanizing turns out to be low after taking into account the benefits provided by this method. The time to perform such protection is a few hours. With all the aforementioned advantages, it is an ecological and standardized protection, performed in accordance with the quality requirements of the PN-EN ISO 1461 standard.